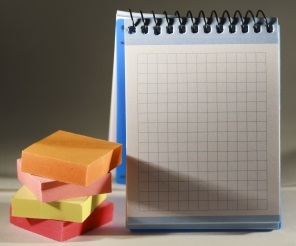
Kaizen, Muda, Gemba, Gent Genbutsu ca-Yoke, Kanban, Jidoka - nu o colecție de greu de pronunțat sunetele.
Toate aceste concepte - baza tehnologiei Lean 6 Sigma. Lumea occidentală nu a îndrăznit să folosească traducerea acestor cuvinte pentru a determina filosofia Lean, nimic nu aventurat și ruso- și lumea ucraineană vorbitoare.
Amintiți-vă, ca într-un film vechi favorit?
Și astfel, în viitor, „pentru a justifica de mare încredere în noi“ și să nu fie prins cu termenii noi și nu întotdeauna ușor de înțeles, astăzi, facem pentru tine o selecție a pieselor principale.
Înțelege, memoreze, si da, va sosi cu Kaizen!
Kaizen. Kaizen, kaydzen (Jap 改善 Kaydzen Kaizen ..) - filozofia japoneza sau practica, care este axat pe îmbunătățirea continuă a proceselor de producție, de dezvoltare, procesele de afaceri de sprijin și de management, precum și toate aspectele vieții.
„Kaizen“ în afaceri - îmbunătățirea continuă de la producție la conducere, de la director la lucrător obișnuit. Prin îmbunătățirea activităților standardizate și procese, scopul Kaizen - producție, fără pierderi.
Cuvântul japonez „Kaizen“ înseamnă „îmbunătățire continuă“. Pe baza strategiei, în procesul de îmbunătățire a tuturor celor implicați - de la manageri lucrătorilor, iar punerea sa în aplicare necesită un cost material relativ scăzut. Kaizen filozofie presupune că viața noastră ca un întreg (muncă, publică și privată) ar trebui să se concentreze pe îmbunătățirea continuă.
Mu'da - aceasta este una dintre cuvântul japonez, ceea ce înseamnă pierderea, deșeuri, adică orice activitate care consumă resurse, dar creează nici o valoare. De exemplu, consumatorii nu au nevoie la produsul finit sau componentele sale au fost în stoc. Cu toate acestea, în sistemul de control convențional al costurilor de depozitare, precum și toate costurile legate de rework, căsătorie, și alte costuri indirecte sunt transmise către consumator.
- pierderile datorate supraproducției;
- pierdere de timp din cauza de așteptare;
- pierdere la transport inutile;
- pierderile datorate etapelor de prelucrare suplimentare;
- pierderile datorate excesului de inventar;
- pierderile datorate mișcărilor inutile;
- pierderile datorate eliberării de produse cu defecte.
De asemenea, a decis să aloce mai multe pierderi de putere 2 - mu'ri și mu'ra care înseamnă, respectiv, „suprasarcină“ și „denivelări“:
Mu'ra - performanțe inegale, de exemplu, programul oscilant cauzate de vibrații nu sfârșitul cererea utilizatorului, ci mai degrabă dispune de un sistem de producție sau ritm neregulat al punerii în aplicare a operațiunii, forțând operatorii să se grăbească mai întâi, și apoi așteptați. În multe cazuri, managerii sunt capabili de a elimina denivelările din cauza alinierii de planificare și atenție la ritmul de lucru.
Mu'ri - echipamente de reîncărcare sau operatorii care apar atunci când se lucrează cu o viteză mai mare sau ritm și cu eforturi mari pe o perioadă lungă de timp - în comparație cu sarcina nominală (standardele de muncă de proiect).
Gemba Gent Genbutsu
Gemba (Jap 現場 Gemba.) - un termen care desemnează un loc în care sunt furnizate produse sau servicii este format. Ideea de Gemba în conducerea întreprinderii este denumit Genbutsu ca Genchi (Jap 現 地 現 物 - vino și vezi.): Pentru o înțelegere completă a situației, este necesar să vină la Gemba - zona în care procesul de lucru - pentru a aduna faptele și la fața locului pentru a lua o decizie.
Foolproof - protecția obiectelor de utilizare (în special, echipamente), software-ul, etc. acțiuni în mod evident incorecte de către o persoană, ca în timpul utilizării, și în timpul întreținerii sau al fabricării. Conceptul a fost dezvoltat și apoi rafinate prin Shigeo Shingo (Shigeo Shingo), inginer de producție japoneză, care odată ce a creat sistemul de producție Toyota.
JIT (Just-in-time)
JIT (Just In Time, JIT) - cea mai frecventă în lumea conceptului de logistică. Ideea principală a conceptului a ansamblului de combustibil este după cum urmează: în cazul în care programul de producție este stabilit, este posibil să se organizeze mișcarea fluxurilor de materiale, ca toate materialele, componente și produse semifinite vor fi primite în cantitatea necesară, la locul potrivit și exact la momentul desemnat pentru fabricarea, asamblarea și vânzarea de produse finite . În acest caz, nu sunt necesare rezervele de asigurare, înghețarea fondurilor companiei. JIT este, de asemenea, unul dintre principiile de bază ale Lean Manufacturing.
Kanban (kamban) - un sistem de producție și de furnizare, care să permită punerea în aplicare a principiului "just in time" (sau "tocmai la timp", Just-in-time).
din lume, dezvoltate și puse în aplicare în primul rând de „Toyota“. În 1959 „Toyota“ a inceput sa experimenteze cu sistemul Kanban și în 1962 a început procesul de transfer al întregii producții la acest principiu. La centrul Kanban sunt constructe teoretice Frederika Teylora, Genri Forda.
Organizarea producției firmei „Toyota“ este un plan anual de producție și a vânzărilor de automobile, care sunt elaborate pe baza planurilor operaționale lunare și a producției medii zilnice la fiecare site, pe baza de predicție a cererii de consum (în timpul preemțiune - 1 și 3 luni). programele de producție de zi cu zi sunt făcute doar pentru linia de asamblare principală. Pentru magazine și site-uri care deservesc transportorul principal, programele de producție nu sunt pregătite (acestea sunt stabilite volumele de producție lunare doar orientative).
Utilizarea constantă a filozofiei de „just in time“ poate dezvălui nedescoperit până acum defecte. Stocurile sunt foarte bine potrivite pentru ascunderea defectelor. Numai cu o scădere a stocurilor poate vedea problema. Acest lucru este foarte similar cu modul ridicat nivelul apei se ascunde recife subacvatice.
„Kanban“ - în japoneză înseamnă card.
Jidoka (Jap -. Calitatea Încorporarea) - principiul autonomizării (autonomation), sau automatizarea cu folosirea inteligenței.
Acesta nu trebuie confundat cu automatizare convențională (automatizare). Autonomizare uneori numit de automatizare a elementului de informații, sau „automatizare cu o față umană.“ Autonomizare îndeplinește un rol dublu. Se elimina supraproducție, o componentă importantă a pierderilor de producție, și previne producerea de produse cu defecte.
SMED (conversie rapidă)
trecerea rapida (SMED ;. Single-Minute Schimb de Dies - literalmente „matrițe de schimbare rapidă“) - schimbare / retehnologizare a echipamentelor în mai puțin de 10 minute.
SMED - o abreviere de schimb Minut unic ștanțelor (schimbarea rapidă a matrițelor). De fapt, sistemul SMED - un set de metode teoretice și practice care reduc timpul de instalare și operațiunilor de schimbare de până la zece minute. Inițial, acest sistem a fost proiectat pentru a optimiza operația de înlocuire mor, și resetarea echipamentului adecvat, dar principiile de „schimbare rapidă“ poate fi aplicat tuturor tipurilor de procese.
Shigeo Shingo a luat nouăsprezece ani pentru a dezvolta sistemul SMED. Studierea trecerea de operare în multe plante, el a descoperit două lucruri importante care au stat la baza SMED:
- acțiune intern privind trecerea, adică, operațiunile care sunt efectuate după oprirea echipamentului. De exemplu, matrița poate fi înlocuit numai atunci când presa este oprită.
- Acțiuni externe prin schimbarea monetară, și anume operațiunile care pot fi efectuate în timpul funcționării. De exemplu, șuruburi mucegai pot alege și aranja presei în timpul funcționării.
2. Conversia cât mai multe operațiuni interne pentru a permite mai multor externe de schimbare ori pentru a reduce timpul de schimbare.
Unul dintre primele experimente, punerea în aplicare a sistemului SMED în procesul de producție a companiei Toyota a dovedit că presa trecerea mai mult de 1000 de tone nu se poate efectua în patru ore, așa cum sa întâmplat și în doar trei minute. Viteza de schimbare este important pentru orice companie care caută să construiască procesul de fabricație pe principiile „tocmai la timp“, și producția de loturi mici. schimbare rapidă pentru aceste companii oferă posibilitatea de a schimba rapid intervalul și pentru a evita acumularea de stocuri excedentare de produse în stoc.
Sistemul SMED - cea mai eficientă abordare pentru a reduce timpul de schimbare. Cu acest sistem va fi capabil de a reduce în mod semnificativ cantitatea de activități complexe, lungi și neproductive privind trecerea echipamentelor, în cazul în care nu a scăpa de ele, care, desigur, va facilita nu numai munca în persoană, dar, de asemenea, face compania dumneavoastră mai competitivă.
5S - Sistem de raționalizare la locul de muncă. Acesta a fost dezvoltat în post-război Japonia, la compania Toyota.
5C - cele cinci cuvinte japoneze:
Unele formulare înșelătoare a conceptului.
5S - nu este doar o „standardizare de curățare.“ 5S - o filozofie de low-cost, de producție de succes, macră.
Acest concept filozofie / producție înseamnă că fiecare angajat al întreprinderii de curățare directorului și a efectua aceste 5 reguli simple.