Tema sarcinilor individuale: „Construirea unui diagnostic de sisteme de acționare hidraulice“
Hidraulic - un set de dispozitive destinate mașinilor de propulsare de energie hidraulică. Elementele obligatorii sunt pompe hidraulice de acționare și un motor hidraulic [1, c.148].
Pentru a muta organismele de lucru ale echipamentului metalurgic, precum și alte industrii și, în special, pentru a efectua spate - mișcarea înainte a organelor de lucru sunt utilizate pe scară largă unități hidraulice, în special în cazurile în care sunt necesare eforturi semnificative în organele de lucru ale mașinii de mici dimensiuni de gabarit conduce, finețe mare în mișcare și fiabilitatea de funcționare. Aplicarea servomotoare hidraulice corespunzătoare și când este necesar să se asigure un control fără trepte al vitezei, și o frecvență ridicată de inversare de control automat.
Aplicarea pe scară largă a primit hidraulic controlat mecanic (actuator hidromecanic) constând din tipul actuatorului distribuitor cu sertar cilindric într-un cilindru hidraulic, precum și de intrare și de control al puterii de ieșire tije. Aceste unități sunt proiectate pentru a muta manual sau automat elementul controlat.
În funcție de principiul de funcționare al elementelor de acționare hidraulice mecanism de reglare hidraulic sunt împărțite în mișcare de rotație și de translație. Mișcarea de rotație hidraulică motoare actuatoare sunt folosite și în mișcare de translație hidraulică - cilindri hidraulici. Multe unități și părți ale acestor unități, inclusiv motoare si piese, au multe în comun în proiectarea și relațiile tehnologice. Cele mai utilizate pe scară largă ca hidrotransmisiuni mișcarea de translație, caracterizată prin simplitate, fiabilitate ridicată și manufacturability de desene sau modele.
Avantajele și dezavantajele sistemelor hidraulice
Plusuri hidraulic [1, c.150], [2, C.15]:
1. Transferul de forțe mari, într-un spațiu mic.
2. densitate ridicată de energie.
3. Posibilitatea de stocare a energiei.
4. Schimbarea fără probleme a valorilor forță motrice (viteza, forțe, momente, și așa mai departe).
5. controlabilitate rezultate bune forțe.
6. Modul rapid inversă datorită maselor mici (moment minor de inerție) ale elementelor de antrenare.
7. Dinamica mare de comutare.
8. mișcare uniformă (fără vibrații, și netensionată).
9. Gama de transmisie mare.
10. Un mod simplu de a transforma mișcarea de rotație în mișcare rectilinie, sau invers.
11. discreție constructivă, atunci când introduce elemente structurale.
12. Separarea spațială a puterii de antrenare și de evacuare prin conducte și furtunuri.
13. Capacitatea de a automatiza toate tipurile de mișcări și mișcări cu ajutorul unor valve de control auxiliare și de comandă transmisie electrică.
14. Posibilitatea de a utiliza elemente și grupuri de elemente combinate structural standard.
15. Protecție împotriva suprasarcinilor.
16. Ușor de uzură, deoarece elementele hidraulice de lubrifiere se realizează de către mediul de lucru.
17. Durabilitate ridicată.
18. Posibilitatea de recuperare a energiei.
Dezavantaje hidraulice [1, c.151], [2, C.15]:
1. Pierderea de presiune și presiunea (frecare lichid) prin conducte și administrare.
2. Dependența viscozității de temperatură și presiune.
3. compresibilitatea fluidului.
4. fluid de lucru Uchechki prin etanșare spațiu liber și, în special la presiuni ridicate.
5. Eficiența inferioară (pentru motivele prezentate mai sus), decât în transmisii mecanice comparabile.
6. Necesitatea de a se asigura că, în timpul funcționării puritatea fluidului de lucru și de protecție împotriva pătrunderii aerului.
7. Pozharoopasnot în cazul unui fluid de lucru combustibil.
Principalele elemente și eșec hidraulic
Principalele elemente din mașinile de oțel hidraulice care necesită depanare și cauzează defecțiuni în condițiile de funcționare sunt pompe, supape, motoare, cilindri hidraulici, preaplin și siguranță supapele [3, c.197]. Ca urmare, suprafața de uzură a pompei de împerechere scade randamentul volumetric ceea ce reduce eficiența unității pompei ca un întreg. Atunci când un supape de control a erorilor și a cilindrilor hidraulici de scurgere a crescut de scurgere internă și externă a fluidului de lucru care reduce, de asemenea, randamentul volumetric sisteme hidraulice. Aceste defecte determină liniile hidraulice zgomot, vibrații, loviri, creșterea temperaturii lichidului și așa mai departe. Eșecul mașinilor de acționare hidraulice necesită diagnosticare rapidă și imediată de luare a deciziilor.
Anumite tipuri de stări defecte ale sistemului hidraulic [4]:
- presiunea în conducta de alimentare nu se încadrează în specificații;
- forța de presiune depășește admisibilă pe autostradă;
- furnizarea de pompe hidraulice mai puțin acceptabile;
- scurgere externă depășește admisibilă;
- pulsația de presiune a pompei hidraulice depășește admisibilă;
- cantitatea de lichid hidraulic din rezervorul hidraulic este mai mică decât admisibilă;
- forța de frecare de acționare deasupra admisibilă;
- pierderi de presiune în unitatea hidraulică de mai sus admisă;
- poluarea fluidului de lucru mai mare decât cea permisă;
- temperatura fluidului de lucru mai mare decât cea permisă.
Se determină vina în două moduri:
- prin simțuri;
- cu ajutorul unor instrumente și unelte.
Cel mai simplu eșec al sistemului hidraulic poate fi detectat prin simțuri - vederea, auzul, senzație. În practică, multe probleme pot fi rezolvate în acest fel, fără utilizarea oricărui tip de unelte, dispozitive și echipamente. Dacă utilizați simțurile nu sunt în măsură să identifice problema, este necesar să se utilizeze dispozitive: manometre, debitmetre, și așa mai departe.
Diagrama schematică a unității hidraulice de mișcare alternativă - lucru membru mișcare de translație este prezentată în Figura 1 [3, C.13].
Figura 1 - Diagrama schematică a circuitului:
1 - motor electric; 2 - Pompă; 3 - conductă; 4 - supapă de siguranță; 5 - rezervor; 6 - cilindri; 7 - pistonul; 8 - mărfurile; 9 - valve; 10 - sugrumare
Principiul de funcționare al unității hidraulice (Figura 1).
Pompa 2 acționat de motorul 1, suge lichidul din rezervorul 5 și îl pompează prin conducta 3 în cilindrul 6 prin supapa 9 și 10. Situat la capătul conductei 7, pistonul rezistă mișcării lichidului. Presiunea în cavitatea „b“ crește atâta timp cât nu există nici o rezistență pentru a depăși pistonul și pistonul 8 cu sarcina nu se va muta. Pentru a proteja sistemul de suprasarcină (pentru a preveni o creștere a presiunii în sistem peste un nivel maxim prestabilit), supapa de siguranță 4 este amplasat într-un astfel de arc de supapă presează mecanic mingea împotriva scaunului supapei, iar actele de linie la presiune existente pe suprafața bilei. Robinetul cu bilă se deschide atunci când forța de presiune a fluidului care acționează pe minge depăși forța arcului. Din acest moment, presiunea nu mai crește pe măsură ce fluidul este pompat în rezervorul este golit. Direcția de mișcare a pistonului comandă supapa 9. Dacă schimbarea poziției șinei glisant pot fi îmbinate conductele A și P. În acest caz, lichidul care curge prin supapa din pompa în cavitatea „a“. Pistonul se deplasează în jos și sarcina este coborâtă. Lichidul din „b“ intră în camera prin intermediul distribuitorului 5 din rezervor.
Determinarea de diagnostica tehnică, obiective și sarcini de diagnosticare a unității hidraulice
Sistemul de diagnosticare tehnică - un set de monitorizare automată a performanței și depanarea de căutare sistemelor hidraulice [3, c.197].
Scopul diagnosticului - pentru a îmbunătăți fiabilitatea echipamentelor metalurgice. Eșecurile masini si mecanisme atrage după sine consecințe grave, cum ar fi pierderea producției, creșterea consumului de piese de schimb, materiale, energie, resurse de muncă. metode tehnice de diagnosticare permit detectarea defectelor fără demontarea și deteriorări mecanice, pentru a studia dinamica dezvoltării lor în timp util pregătirea și punerea în aplicare a soluțiilor tehnice care împiedică eșecuri [6], c.266.
In dezvoltarea de diagnosticare de mașini hidraulice conduce sistem rezolvă următoarele probleme:
- dezvoltarea unor algoritmi de diagnostic servomotoare hidraulice;
- prezicerea schimba starea lor tehnică în timpul funcționării;
- alegerea metodelor de diagnostic;
- mijloace de diagnosticare pentru dezvoltare [5].
În timpul diagnosticele tehnice de fază operațională contribuie la soluționarea următoarelor sarcini:
- stabilirea prezenței sau a lipsei unui element obiect diagnostic defect și identificarea erorilor făcute în timpul asamblării;
- evaluarea performanțelor mașinilor înainte de punerea lor în funcțiune, după reparații;
- detectarea defectelor care apar în timpul de funcționare.
Selectarea instrumentelor de măsurare și diagnosticare
Selectarea sistemului de măsurare
Diverse istrument folosite pentru a diagnostica hidraulice de acționare, aparate și echipamente. Pentru a stabili un impact asupra fluxului de semnal fluxului de putere, este necesar să se măsoare parametrii regimului de funcționare, în care primii parametri măsurabili hidraulici primite (presiune, debit, temperatura, etc.). Noi trebuie să fie, de asemenea, parametri mecanici măsurabili: deplasare, forță, viteză, viteză sau accelerație.
Selectarea măsurarea se face pe următoarele criterii:
- precizia necesară;
- intervalul de temperatură admisibilă;
- superioară și frecvența limită inferioară;
- interval de presiune admisibilă;
- distanța dintre senzor și procesarea datelor de măsurare;
- comportamentul în ceea ce privește influențele de mediu;
- disponibilitatea tipurilor adecvate;
Elementele sensibile de senzori trebuie să fie de construcție simplă, necostisitoare și interschimbabile, și ar trebui să poată utilizarea lor pe scară largă [2, C.27].
instrumente de diagnosticare tehnică sunt sisteme de măsurare-informare, și sunt folosite pentru a determina starea sistemelor tehnice. Acestea includ mijloace hardware, software și documentație tehnică și operațională [5]. diagnostic instrumente tehnice (TSD), care includ soluții instrumentale și software unitate combinată de diagnostica tehnică de probleme cu o anumită certitudine.
TSD în funcție de scopul sistemelor de diagnosticare concepute pentru următoarele sarcini:
- determinarea eficienței (serviceability, care funcționează în mod corespunzător);
- modificări de prognozare în stat;
- determinarea eficienței și detectării defectelor;
- determinarea și predicția eficienței;
- evaluarea performanței, detectarea defectelor și predicția modificărilor în stat.
În cazul cel mai general al structurii tehnice a sistemului de diagnosticare include următoarele unități:
- senzori care permit conversia diferitelor mărimi fizice în semnale electrice;
- trecerea la asigurarea conectivității diferitelor cantități de un program specific;
- o memorie pentru stocarea valorilor de referință ale toleranțelor, rezultatele intermediare;
- indicarea și înregistrarea pentru afișarea rezultatelor obținute prin efectuarea procedurilor de măsurare, monitorizare, diagnosticarea și de calcul;
- prelucrare, în care suma operațiunilor poate fi variată într-o gamă largă de operații logice simple, ca rezultat emiterea de către parametrul de control generalizat la calcule complexe la determinarea dependențe funcționale în timpul rezolvării problemelor de măsurare sau de predicție (extrapolarea) în timpul diagnosticului. Pentru punerea în aplicare, înseamnă calcul unitate de procesare implicate;
- Controlul care pune în aplicare programul adoptat de diagnostic.
Să considerăm, de exemplu, un set de echipamente pentru diagnosticarea și ajustarea SDM-6-450 (Figura 2) [7].
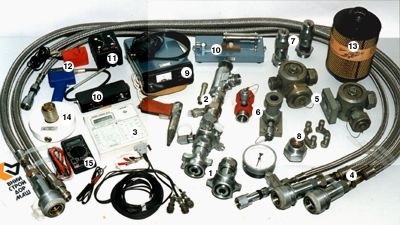
Figura 2 - Un set de echipament pentru diagnosticare și configurare SDM-6-450:
1 - gidrotester universală; senzori de debit, presiunea, temperatura și viteza unui arbore motor diesel - 2; 3 - microprocesor electronic; 4 - conectarea manșoane; supapă cu trei căi - 5; 6 - adaptor; 7 - Tub rezbovye pentru evacuarea fluidului de lucru în rezervor; 8 - supape; 9 - detector de scurgeri cu ultrasunete; 10 - blocuri de control „knocking“ de compuși și de calibrare; 11 - baterie; 12 - indicatorul contaminării fluidului cu adaptor; 13 - filtru magnetic; 14 - un dispozitiv pentru setarea senzorului de viteză de rotație pe arborele cardanic; 15 - metru.
Acest echipament vă permite să:
- măsurarea pompelor de alimentare și de curgere în elementele de acționare hidraulice (10 - 400 l / min), scurgerea internă a temperaturii fluidului de lucru, presiunea în conductele hidraulice (0,5 - de 40 MPa), turația arborelui motor diesel (100 - 6000 rot / min);
- configura în mod individual supapele de siguranță a presiunii primare și secundare;
- găsirea unui loc scurgeri interne în conductele hidraulice și să evalueze valoarea acestora;
- diagnosticarea nu mai puțin de 250 de vehicule pe an;
- prezice funcționarea fiabilă a unității hidraulice.
Pentru a diagnostica unitatea hidraulică este de asemenea recomandabil să se utilizeze kitul de diagnosticare „Gidrotester HT-600M“ (Figura 3) [8].
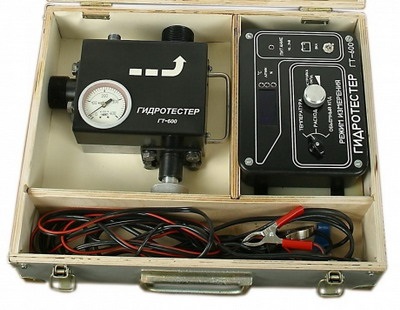
Figura 3 - vedere generală gidrotestera GT - 600M
Acesta este destinat să determine starea tehnică a unităților hidraulice în mașini hidraulice, mașini-unelte, macarale, laminoare, prese și echipamente pentru diverse scopuri.
Luați în considerare algoritmul de diagnostic al unității de pompare.
Figura 4 este o diagramă a unui sistem de diagnosticare a unității de pompare a unui laminor cu un dedicat unități de pompare operator de la distanță și principala moara consola de control.
Figura 4 - Telecomanda și diagnosticare
Parametrii generali de diagnosticare sunt presiunea uleiului din sistemul hidraulic, temperatura și nivelul uleiului din rezervor, starea filtrului, faptul activa și dezactiva elementele hidraulice. Temperatura, presiunea și nivelul uleiului sunt determinate de către senzorii instalați în punctele monitorizate, precum și faptul că unitățile și oprirea pompelor și echipamente hidraulice se determină cu ajutorul senzorilor de poziție sau a contactelor în circuitul electric care controlează circuitele de acționare a pompelor.
Sistemul funcționează după cum urmează.
Pe panoul sunt activate permanent lampa care indică nivelul și temperatura uleiului din rezervor, filtru de colmatare, poziția pompei de circulație (pornit, oprit). Dacă este necesar, sistemul de încălzire ulei este pornit. Dacă acești parametri ai sistemului hidraulic este normal, folosind operatorul cheie poate asambla pentru a activa schemele electrice de la unități de pompă. Pe măsură ce lămpile indicatoare de scheme de pregătire. Pornirea pompelor de antrenare (cu orice număr de instruit pentru a rula), se realizează cu ajutorul unui comutator special. De asemenea, folosind un singur comutator, în același timp, opriți toate pompele. Parcurgerea cu succes a operațiilor indicate cu lămpi de semnalizare. Nu a fost exclus de pe orice unitate de pompă cu ajutorul cheii. Presiunea din sistemul hidraulic este controlat de un senzor de presiune și indicate prin avertizare lumini de pe consola la trei poziții (presiune normală, de joasă presiune, presiune prea scăzută). La presiune scăzută și foarte scăzută, ceea ce indică eșecul în pompele hidraulice pot fi oprite. Pompele sunt dezactivate atunci când nivelul lichidului din rezervor sub „Fill.“ Nivelul Excesul de ulei din rezervor indică o defecțiune în sistem, atunci nu poate rula pompele. În acest caz, o alarmă sonoră [3, c.198].
În prezent, metalurgice, miniere și alte industrii și sisteme hidraulice de acționare hidraulică sunt utilizate din ce în ce. Mijloacele ar trebui dezvoltate modalități de a diagnostica, un serviciu. Toate acestea implică proiectarea și punerea în aplicare a sistemelor de acționare hidraulică de încercare. Utilizarea acestor sisteme va: furniza monitorizarea stării și depanarea elementelor de acționare hidraulice; reducerea pierderilor de producție și a consumului de resurse materiale și de muncă; a îmbunătăți fiabilitatea echipamentului.
REFERINȚE
ADVANCED INTERNET - SURSE