Granularea - proces de conversie material pulverulent într-o anumită valoare de cereale.
Granularea este necesară pentru a îmbunătăți capacitatea de curgere tabletirue- greutatea mea și a preveni exfolierea. În prezent, metodele de granulare existente sunt împărțite în următoarele tipuri principale:
0 granulare uscată;
0 granulare umedă (granulare prin împingere);
0 bloc granulare.
Granularea uscată este o comprimare a produsului uscat, formarea plăcii sau preformă, care este apoi zdrobit în granule de mărimea dorită.
În particule uscate de granulare kompaktiruyuteya (compactate) de la punctele de contact, apoi unele dintre ele se descompun în cele mai mici, care umplu porii dintre particule, care contribuie la compactarea în continuare a masei presate.
În acele cazuri în care substanța medicamentoasă în prezența apei, sau în timpul uscării intră în reacție chimică sau suferă modificări fizice (topire, înmuiere, schimbarea culorii) utilizând granulare uscată.
In prezent, granularea uscată, în caz de rezistență insuficientă a granulelor de pulbere introdusă în masa presată, lianți uscați (celuloză microcristalină, oxid de polietilenă), pentru a asigura aderența particulelor sub presiune atât substanțe hidrofile și hidrofobe.
granularea uscată medie se realizează pe rolele orizontale mecanice, arcurile comprimabile sau pistonul hidraulic. In aceasta masa granulată este trecut între role într-o bandă continuă, care este apoi mărunțit și cernut printr-o placă perforată cu o dimensiune a ochiurilor dorită.
Granularea uscată în industria farmaceutică este produsă folosind granule de tip 3027 (Mariupol OST).
Metoda de granulare umedă - frecare masa umedă printr-o suprafață perforată pentru compactare pulbere și obținerea de granule uniforme, granule, având o bună fluiditate. Aceeași metodă a fost tratată de pulberi cu Fluiditate slabă și insuficientă între coeziunea particulelor.
Etapa de granulare umedă cuprinde următoarele operații: măcinare; amestecarea pulberilor; umezirea pulberi soluții de lianți și amestecare; granularea masa umedă; uscarea granulatului umed; procesarea granulelor uscate.
Măcinarea substanța medicamentoasă utilizată pentru a realiza o amestecare uniformă, eliminând agregate mari
lipite împreună și bulgări de materiale, îmbunătățirea funcțiilor biologice.
Sub măcinare mecanică înțeleagă procesul de divizare a particulelor solide înainte de conversia acestora în pulbere, prin aceasta crescând considerabil suprafața totală a materialelor zdrobite, și în consecință biodostupnosg lor. De exemplu, reducerea dimensiunii particulelor de griseofulvina de la 100-200 microni la 2-5 crește eficiența sa jumătate. Cu toate acestea, micronizarea de droguri, în ciuda unei posibile creșteri biodisponibilitate, nu a găsit o largă utilizare în formulări tehnologice solide, cu excepția unor cazuri. Acest lucru poate fi explicat prin faptul că cristalele sunt structura formate rigid cu energie internă minimă liberă și ridicată. Prin urmare, pentru distrugerea ei necesită forțe externe semnificative. In sistemul de cristal, simultan cu frecare îmbunătățită de măcinare reducând sarcina aplicată la o valoare capabilă să provoace o mică deformare elastică sau plastic. Prin urmare, eficiența de măcinare, în special în materialele cristaline, cu punct de topire ridicat, scade rapid. Pulbere Pentru a crește deformarea plastică care urmează să fie măcinat este introdus într-o fază lichidă.
Atunci când măcinarea o creștere a energiei libere a cristalului poate sposobostvovat substanțe de degradare mecano și reduce astfel stabilitatea lor de depozitare.
Milling materiale superplastic cu puncte de topire scăzute (cum ar fi agenți de alunecare și lubrifianți) poate conduce la o creștere semnificativă a eficienței lor în prepararea tabletelor.
Amestecarea pulberilor se face în scopul realizării unei tabletării mase omogene, precizia de dozare și distribuție uniformă a substanței active în comprimate. Pentru amestecarea și umectarea pulberilor amestecătoare utilizate, care prin design pot cădea în mai multe grupe: mixere cu palete rotative; șurub mixere; tobe mixte.
Atunci când amestecarea pulberilor trebuie să respecte următoarele reguli:
0 pentru mai adăuga minim;
0 substanțe potenți și toxice utilizate în cantități mici, au trecut în prealabil printr-o sită, se adaugă la greutatea porțiunilor individuale sub formă de triturare, adică diluarea cu excipient într-o concentrație de 1: 100;
0 substanțe și substanțe cu greutate specifică ridicată colorate este încărcat în amestecător în ultimă instanță;
0 nu poate fi administrat ulei esențial volatil în masa de amestecare, deoarece în timpul amestecării ele se evapora. Aceste substanțe sunt introduse într-un granulat uscat în masă înainte de comprimare într-o etapă de prăfuire.
Practica fabricarea tabletelor indică faptul că timpul necesar pentru amestecare rețetă simplă (cu două și trei componente) în stare uscată, 5-7 min, mai complex - 10-12 minute. După amestecarea pulberilor uscate din greutatea umectant adăugat în porțiuni. Prezentarea unui umidificator cu mese ospitalitate nevoie pentru a preveni masa aglutinarea. Prin utilizarea umectanți se realizează posibilitatea umectarea pulberilor nonwettable cu apă.
Cele mai eficiente și durabile Lianții sunt derivați de celuloză: metiltseyalyuloza, hidroxipropil metilceluloza, karboksimetiltsellyudoza de sodiu, precum alcool polivinilic, polivinilpirolidonă; Este considerat gelatină mai puțin eficientă, amidon și derivații săi.
În pulberile de amestecare umede uniformitatea distribuției lor este mult îmbunătățită, nu se observă separarea particulelor de pulbere și greutatea mănunchiului, îmbunătățește ductilitate acestuia. Amestecarea pulberii umectată este însoțită de o anumită masă de etanșare din cauza deplasării aerului, care permite obținerea unei granule solide mai dense. Timpul de amestecare pentru amestecuri umede simple, în masă este de 7-10 m, pentru complex - 15-20 de minute.
Cantitatea optimă a umidificatorului este determinat în prealabil experimental pe baza proprietăților fizico-chimice ale pulberilor și este specificată în regulamentele. Eroare la calcularea umidificatorului poate duce la căsătorie dacă umidificatorul de a introduce pelete mici după uscare se va prăbuși, iar dacă o mulțime de masă va fi granulare vâscos și slab.
Greutate cu conținut optim de umiditate este un amestec umed, compact nu aderă la mână, dar atunci când sunt strivite cu dezintegrare în bucăți separate.
masa de granulare umedă este produsă pe mașini speciale - granulatoare, al cărui principiu constă în lame că materialul este șters (role elastice sau alte dispozitive) prin cilindru perforat sau plasă. Granulatoare sunt verticale și orizontale. Pentru a asigura procesul de ștergere a mașinii ar trebui să ruleze în mod optim, fără supraîncărcare, astfel încât masa umedă pentru a trece liber prin alezajul cilindrului sau grila. Dacă masa este suficient de hidratat și gradul de plastic, aceasta nu se va sigila gauri si procesul frecare se realizează fără dificultate.
În cazul în care masa vâscoasă și sigilate gaura, aparatul are o suprasarcină și necesitatea de a se transforma periodic de pe motor și se spală lamele tambur.
Selectarea granularea sită este de mare importanță. Se constată că masa umedă trebuie să treacă printr-o sită cu diametrul găurii de 3-5 mm, și uscat - printr-o sită cu diametrul găurii de 1-2 mm.
Pentru granularea amestecurilor de tablete cu scopul de a pregăti pentru tabletare în metoda ultimii ani fluidizării este utilizat pe scară largă în industria farmaceutică internă și externă. Principala caracteristică a acestuia este faptul că materialul care trebuie tratat, iar apoi granulele rezultate sunt în mod continuu în mișcare. Principalele procese - amestecare a componentelor, soluția umezirea amestecului de laminare, granulare, uscare și granulat ce intră prăfuire - să aibă loc într-un singur aparat.
Formarea și creșterea granulelor în patul fluidizat are loc prin intermediul a două procese fizice: comasare după umectare și drenarea aglomerare. Calitatea peletelor și compoziția lor fracționată depind de mai mulți factori care determină cursul procesului. Principalele sunt viteza fluidiza compoziția gazului și viteza de lichid de granulare, temperatura din patul de curgere.
Atunci când amestecurile de granulare comprimat în patul fluidizat este amestecarea prima etapă de proces, care afectează calitatea unui granulat. Uniformitatea amestecare depinde de modul de operare al vehiculului aerodinamic, raportul componentelor din amestec, forma particulelor și densitatea. Pentru a îmbunătăți omogenitatea masei condițiilor de agitare sau sac sub duvki filtre, fără a întrerupe fluidizării.
Atunci când amestecarea particulelor sunt apropiate una de alta în formă și având un raport în greutate mai mic de 1:10, agitarea amestecului are loc fără separare; la un raport mare de caractere agitare în mare măsură depinde de forma și densitatea particulelor și parametrii aerodinamice ale proceselor și necesită un studiu special pentru a selecta modul optim.
La adăugarea lichidului de granulare, masa de granulare particulelor încâlcirea datorate forțelor de încleiere atât lichid și soluția formată după umezire a stratului de suprafață a lichidului material prelucrat. În procesul de uscare a bulgărilor în aglomeratele solide
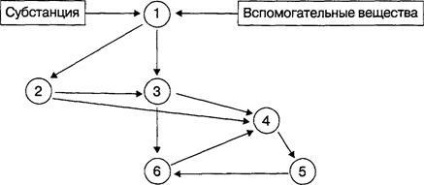
Fig. 22.4. Diagrama schematică a aparatului SG 30-amestecuri tabletării pat fluidizat de granulare
că, ca urmare a frecării între ele și cu pereții aparatului parțial rupt.
Procesul de granulare într-un pat fluidizat are loc simultan cu uscarea, granulele cu aer cald. În acest scop, plantele CIS folosite mașini SG-30 (Fig. 22,4), „Aeromatic“ (Elveția), „Glatt“ (Germania) și altele. În cazul în care, după terminarea amestecului de tabletare granulare având umiditatea reziduală de compresie necesară, o uscare suplimentară nu este necesară.
Pudrare granulat uscat produs în același aparat, cu adaos de material antifricțiune în granule și un amestec secundar într-un pat fluidizat.
Produsul granulat obținut în patul fluid are o serie de avantaje față de granulat obținut prin granularea umidificat mecanică: formă mai rotunjită de granule, fluiditate mai bună, compoziția fracționată mai echilibrată.
Pentru a asigura calitatea formelor de dozare solide este mult afectată de condițiile de uscare a granulatului umed.
Uscarea granulatului umed se efectuează:
uscător 0 tava cu circulație forțată a aerului;
0 cuptoare cu o coloană cu silicagel.
Când uscarea într-o grosime uscător tavă nu trebuie să depășească 2-2,5 cm. Diametrul maxim de cereale nu trebuie să fie mai mare de 5 mm.
În străinătate utilizate pe scară largă companii uscător de „Munster“, „Aeromatic“ și altele. Uscătoare funcționează după cum urmează.
Fluxul de aer aspirat în partea superioară a cadrului ventilatorului, este încălzit în aer cald la o temperatură predeterminată, este curățată în filtru și se duce direct în uscător, în cazul în care produsul prin recipient, din produsul în sus de jos strat fluidizant. aer suplimentar umidificat trece prin filtru sac, purificat din particule mici de produs și evacuată în atmosferă. Principalul lor avantaj - de înaltă performanță. Timpul de uscare a materialului, în funcție de proprietățile sale fizice și forma dureaza 20-50 min. Astfel de uscătoare protreb- lyayut puțină putere și ocupă o zonă de lucru mică.
Granulele uscate înainte de comprimare trebuie să aibă un anumit conținut de umiditate, ceea ce se numește un reziduu. Reziduale mase tabletării umiditate pentru fiecare individ și ar trebui să fie optimă, adică una în care are loc procesul de compresie bine, calitatea tabletelor îndeplinesc cerințele GF și puterea lor cea mai mare, comparativ cu tabletele derivate din granulele din același medicament, cu diferite grade de umiditate. granule Nedosushennye adere la pumni, matrice neuniform umplut și creează necesitatea unor cantități crescute de material anti-fricțiune. pelete si tablete presate Excesiv tare sunt adesea obținute cu margini rupte. Produsul uscat a fost peletizat din nou la o distribuție de umiditate uniformă și distribuția dimensiunii particulelor în granulat, aproape de normal.
Granularea structural mai promițătoare, formarea de pelete rotunjite și care asigură în mod uniform de dimensiuni, ceea ce îmbunătățește calitatea tabletelor, îmbunătățește precizia de dozare a medicamentului. Pentru granulare de granulație structurală includ uscarea prin pulverizare și cuvă de acoperire granulare.
Atunci când este produsă prin granulare prin pulverizare granulatului se realizează prin pulverizarea în auxiliarii de suspensie de uscare prin pulverizare și umidificator. Apoi, granulele obținute au fost amestecate cu substanțe medicamentoase și, dacă este necesar, se adaugă substanțe auxiliare care nu au fost anterior plasate în pastă. Acest tip de granulare este recomandabil să se aplice în cazurile în care contactul prelungit al produsului granular cu aer nu este de dorit (de exemplu, în producerea de enzime, antibiotice, produse de origine animală și vegetală materii prime).
Pentru tigai de acoperire granulare de dozare și dispozitivele auxiliare necesare au fost încărcați într-o cuvă de acoperire și în timpul rotației sale umidificarea produce, și apoi uscarea treptat granulele obținute. Când acest particule de pulbere incleiate și frecarea rezultată dobândi o formă mai mult sau mai puțin regulate.
Structurală se referă la umed metoda de granulare, granularea conduce la formarea de rotunjite, dar în anumite condiții și granule destul de uniform dimensionate. În prezent, trei moduri de a aplica granularea structurale:
0 granulare într-o tavă de acoperire, în care amestecul de pulberi este încărcat deoarece se rotește și să producă hidratare. Particulele de pulbere adunate laolalta, ca urmare a frecării dobândi forma corecta;
0 pulverizare suspensii granulare, care sunt produse într-un pat fluidizat de tip aparat SG, urmată de uscare;
0 granulare într-un pat fluidizat.