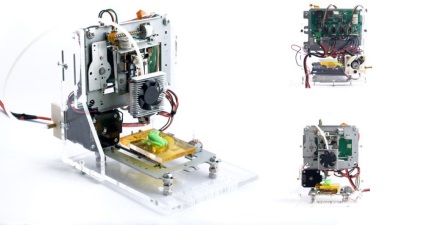
Acest proiect descrie proiectarea bugetului imprimantei 3D cost foarte scăzut, care este în principal construit din componente electronice reciclate.
Rezultatul este o imprimantă de format mic pentru mai puțin de 100 $.
În primul rând, vom afla cum sistemul total CNC (asamblarea și calibrarea, rulmenți, ghiduri) și apoi preda aparatul pentru a răspunde la instrucțiunile G-cod. După aceea, vom adăuga un extruder de plastic mic si da comenzi la extrudare din plastic alimentare cu setări de calibrare conducătorului auto și alte operații care vor da viață la imprimantă. După această instrucțiune veți obține o mică imprimantă 3D, care este construit cu aproximativ 80% din componente reciclate, ceea ce îi conferă un mare potențial și ajută la reducerea semnificativă a costurilor.
Pe de o parte, veți obține o idee de fabricație inginerie și digitale, iar pe de altă parte, veți obține o imprimantă 3D mică este construit din componente electronice reutilizabile. Acest lucru ar trebui să vă ajuta să devină mai experimentat în abordarea problemelor asociate cu eliminarea deșeurilor electronice.
Etapa 1: X, Y și Z.
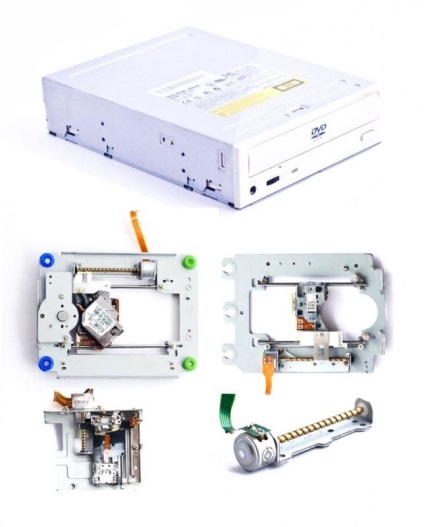
- unitate / DVD 2 CD standard pe vechiul computer.
- 1 unitate de dischetă.
Putem obține aceste componente gratuit, contactați reparațiile centru de service. Dorim să ne asigurăm că motoarele pe care le folosim din unitățile floppy disk sunt motoare pas cu pas și nu motoare de curent continuu.
Etapa 2: Se prepară motorul
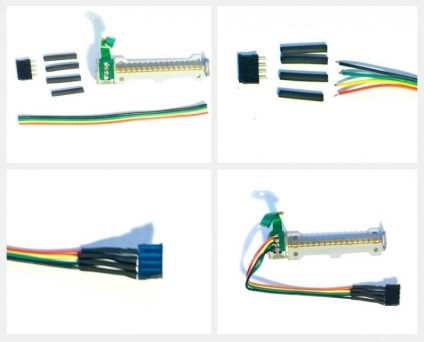
cu motor pas cu pas 3 de pe unitatea CD / DVD.
1 NEMA 17 motor pas cu pas pe care trebuie să cumpere. Noi folosim acest tip de motor pentru extruder de plastic, care au nevoie de o mulțime de efort necesar pentru a lucra cu fire de plastic.
Electronica CNC: platformă sau RepRap Gen 6/7. Este important ca putem folosi Sprinter / Marlin Open Firmware. În acest exemplu, vom folosi electronica RepRap Gen6, dar puteți alege în funcție de preț și disponibilitate.
Cabluri, soclu, psihiatru tub.
Primul lucru pe care vrem să o facem cât mai curând am menționat motoare pas cu pas, suntem capabili de a lipi firele la ea. În acest caz, avem 4 cablu, pentru care avem nevoie pentru a menține secvența de culoare corespunzătoare (descrisă în pașaport).
Specificațiile pentru motoare pas cu pas CD / DVD: Descărcați. Download Mirror.
Specificații pentru NEMA 17 motor pas cu pas: Descărcare. Download Mirror.
Pasul 3: Pregătirea unei surse de alimentare
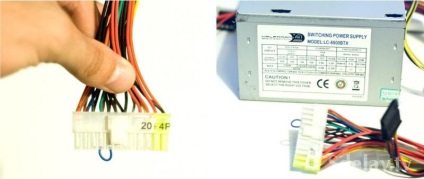
Următorul pas este de a pregăti mâncarea pentru ao utiliza pentru acest proiect. În primul rând, vom conecta două fire împreună (așa cum se arată în figură), pentru a permite alimentarea directă cu un comutator de pe suport. Apoi, vom alege un galben (12V) și un cablu negru (GND) la putere controler.
Pasul 4: Verificați motorul și software-ul Arduino IDE
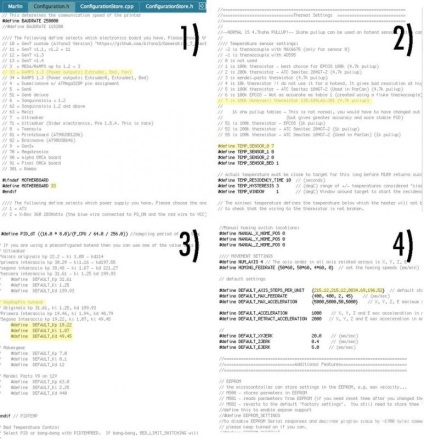
Trebuie să descărcați și să instalați o versiune a Arduino 23.
După aceea trebuie să descărcați firmware-ul. Am ales Marlin (Marlin), care este deja configurat și poate fi descărcat Marlin: Descărcați. Download Mirror.
Odată ce am stabilit Arduino, ne conectam calculatorul nostru cu Rampe / Sanguino / Gen6-7 controler CNC cu un cablu USB, vom alege portul serial corespunzător sub instrumente Arduino IDE / portul serial, și vom alege tipul de plăci controlor în cadrul instrumentelor ( rampe (Arduino Mega 2560), Sanguinololu / Gen6 (Sanguino W / ATmega644P - Sanguino trebuie instalate în interiorul Arduino)).
Principala explicație pentru parametrul, toate setările de configurare sunt fișier configuration.h:
În mediul Arduino, deschidem firmware-ul, deja am descărcat fișierul / Sketchbook / Marlin și vom vedea setările de configurare înainte de a încărca firmware-ul la controlerul nostru.
1) #define MOTHERBOARD 3, în conformitate cu echipamentul actual, folosim (1,3 sau 1,4 Rampe = 33, Gen6 = 5).
2) Termistorul 7, RepRappro utilizează Honeywell 100k.
3) PID - această valoare face cu laser noastră este mai stabilă în ceea ce privește temperatura.
4) Pas pe unitate, acest lucru este foarte important pentru a configura orice controler (Etapa 9)
Pasul 5: Imprimanta. Computer Management.
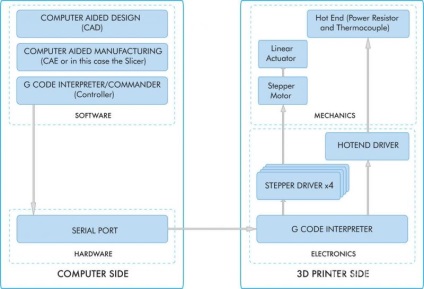
de administrare a imprimantei prin intermediul computerului.
În cazul nostru, ne-am configuret profilul Skeinforge pentru imprimantă, care pot fi integrate în software-ul gazdă cap de înregistrare.
Etapa 6: Reglarea intensității curentului și
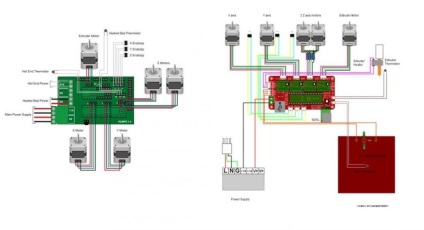
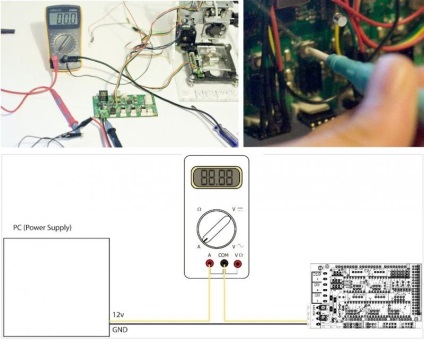
Acum suntem gata pentru a testa motoarele imprimantei. Conectați computerul și de comandă a mașinii cu ajutorul cablului USB (motoare trebuie să fie conectat la mufele corespunzătoare). Start Repetier hosting și activează legătura între software-ul și controlerul selectând portul serial corespunzător. În cazul în care conexiunea este de succes, puteți controla motoarele conectate folosind comanda mâna dreaptă.
Pentru a evita supraîncălzirea motorului în timpul utilizării regulate, vom ajusta puterea curentului la fiecare motor ar putea obține o sarcină uniformă.
Pentru a face acest lucru, vom conecta doar un singur motor. Vom repeta acest proces pentru fiecare axă. Pentru aceasta avem nevoie de un glucometru, atașat în serie între sursa de alimentare și controlerul. Contorul trebuie să fie setat la modul amplificator (curent) - a se vedea figura.
Apoi vom conecta controlerul la computer din nou, porniți-l și măsurați curent cu un multimetru. Când vom activa manual motorul prin interfața Repetier, curentul ar trebui să crească cu un anumit număr de miliamperi (care sunt curent pentru activarea motorului pas cu pas). Pentru fiecare bit axe diferite de curent, în funcție de etapa motorului. Va trebui să înființeze un mic potențiometru pe intervalul treaptă și setați limita de curent pentru fiecare axă în conformitate cu următoarele valori de referință:
Placa conduce un curent de aproximativ 80 mA
Vom furniza curent la 200 mA pentru X și Y axa Steppere.
400 mA pentru axa Z, este necesară datorită putere mai mare de a ridica capul de înregistrare.
400 mA pentru alimentarea motorului extruderului, deoarece este un puternic curent de consum.
Pasul 7: Crearea structurii mașinii
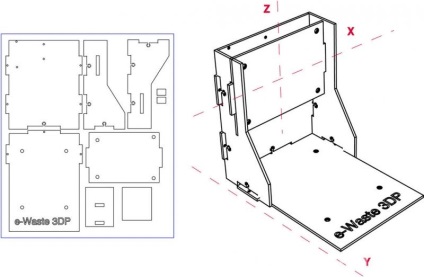
În link-ul de mai jos veți găsi șabloane necesare pentru lasere care taie părți. Am folosit 5 mm grosime placă acrilice, dar pot folosi alte materiale, cum ar fi lemnul, în funcție de disponibilitate și preț.
Tuning cu laser și exemple pentru programul Auto Cad: Descărcarea. Download Mirror.
Construcția cadrului permite să construiască o mașină fără adeziv: toate piesele sunt asamblate cu șuruburi și îmbinări mecanice. Înainte de a tăia cu laser din cadru, asigurați-vă că motorul este bine fixat în unitatea CD / DVD. Va trebui să măsoare și să modifice modelul gaura CAD.
Etapa 8: Calibrarea X, Y și Z axa
Deși standardul Marlin firmware-ului descărcat a fost calibrat pentru axa aveți permisiunea să treacă prin acest pas, dacă doriți să reglați fin imprimanta. Acolo vi se va spune despre firmware-ul care poate fi setat cu laser pas până la milimetru, masina ta are nevoie într-adevăr aceste setări exacte. Această valoare depinde de pașii motorului și dimensiunea filetului tijei în mișcare a axelor tale. Prin aceasta, ne asigurăm că mișcarea mașinii corespunde de fapt, la distanțe de G-cod.
Această cunoaștere vă va permite să construiască o mașină CNC-le, indiferent de tipuri și dimensiuni de componente.
În acest caz, X, Y și Z au aceleași tijele filetate ca valorile de calibrare vor fi aceleași pentru ei (unele pot fi diferite dacă utilizați diferite componente pentru axe diferite).
Va trebui să calculeze cât de mult este necesar pașii motorului pentru a deplasa căruciorul 1 mm. Depinde de:
- Raza scripete.
- Pași pe rotație a motorului nostru pas cu pas.
Parametrii de micro-pas cu pas (în acest caz 1/16, ceea ce înseamnă că, în timpul cu un pas de semnal de ceas se realizează numai 1/16, oferind o mai mare precizie a sistemului).
Am stabilit această valoare în firmware-ul (stepspermillimeter).
Utilizarea interfeței Controler (Repetier) am creat o axa Z, care vă permite să mutați o anumită distanță și pentru a măsura deplasarea reală.
Ca exemplu, vom oferi echipa, asa ca sa mutat la 10 mm și se măsoară deplasarea de 37,4 mm.
Există un număr de pași N definite în stepspermillimeter în firmware (X = 80, Y = 80, Z = 2,560, EXTR = 777,6).
Noua valoare trebuie să fie 682.67.
Repetăm acest lucru timp de 3 sau 4 ori, recompilarea și reîncărcarea firmware pentru controlerul, vom obține o mai mare precizie.
In acest proiect, nu am folosit instalarea finală pentru a face masina mai precise, dar acestea pot fi ușor încorporate în firmware-ul și va fi gata pentru noi.
Suntem gata pentru primul test, putem folosi pen-ul pentru a verifica dacă distanțele în desen este corectă.
Etapa 9: Extruder
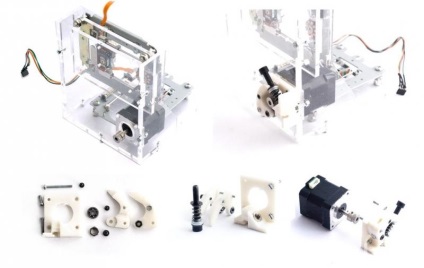
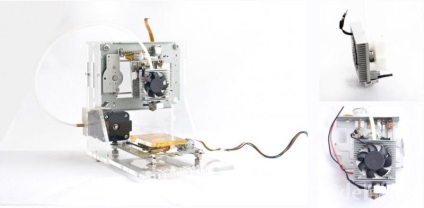
Unitatea pentru filamentul constă dintr-un motor pas cu pas NEMA 17 și MK7 / MK8 pinionului de tip, s-ar putea să-l cumpere. Veți avea nevoie, de asemenea, să aibă un driver pentru a imprima 3D-extruder a fost direct din unitatea, puteți descărca aici.
Filamentul este tras în extruder prin filamentele de control este apoi alimentat în camera de încălzire în interiorul unui tub de teflon flexibil.
Vom colecta unitate directă, așa cum se arată în figură, atașați motor pas cu pas la cadrul principal.
Pentru calibrare, fluxul de plastic trebuie să corespundă filament bucată de plastic și la distanță (de exemplu 100 mm) și a pus o bucată de bandă. Apoi, du-te la software Repetier și apăsați pentru a stoarce 100 mm, distanța și repetați reale Etapa 9 (operația).
Pasul 10: Noi imprimam primul obiect
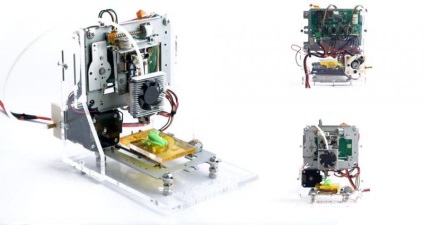
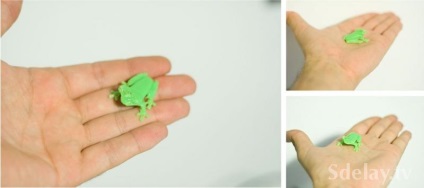
Acum, aparatul ar trebui să fie gata pentru primul test. extruder nostru utilizează un diametru al filamentului din plastic de 1,75 mm, care este mai ușor de a stoarce mai mult și este mai flexibilă decât diametrul standard de 3 mm. Vom folosi PLA din plastic, care este un bio-plastic și are un anumit avantaj față de ABS: se topește la o temperatură mai scăzută, ceea ce face imprimarea mai ușoară.
Acum, în Repetier, activăm tăierea profilurilor care sunt disponibile pentru tăiere Skeinforge. Descărcați. Download Mirror.
Ne imprima pe un cub mic de calibrare a imprimantei (10x10x10 mm), se va imprima foarte repede, și putem găsi probleme de configurare și pierderea de motor pas prin verificarea dimensiunea reală a cubului imprimate.
Deci, pentru a începe imprimarea, deschideți modelul STL și se taie cu ajutorul unui profil standard (sau pe cel descărcat) cu tăiere Skeinforge: vom vedea prezentarea obiectului feliat și G-codul corespunzător. Avem un extruder încălzit, iar când acesta este încălzit până la punctul de topire a materialului plastic (190-210C în funcție de marca de plastic) pentru a stoarce un pic de material (presa de extrudare) pentru a vedea că totul funcționează corect.
Am stabilit originea în raport cu matrița (x = 0, y = 0, Z = 0) utilizat ca separator de hârtie, capul trebuie să fie cât mai aproape de hârtie, dar nu-l atinge. Aceasta va fi poziția de pornire pentru matriță. De acolo putem începe imprimarea.